Con el desarrollo continuo de la construcción de ingeniería subterránea en mi país, hay más y más proyectos de Pit Foundation. El proceso de construcción es relativamente complicado, y el agua subterránea también tendrá un cierto impacto en la seguridad de la construcción. Para garantizar la calidad y seguridad del proyecto, se deben tomar medidas de impermeabilización efectivas durante la construcción de pozos de cimientos profundos para reducir los riesgos traídos al proyecto mediante fugas. Este artículo analiza principalmente la tecnología de impermeabilización de los pozos de base profundos de varios aspectos, incluida la estructura del recinto, la estructura principal y la construcción de capas impermeables.
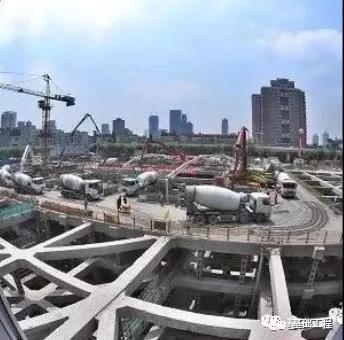
Palabras clave: Foundation Deep Foundation Pit Waterpusting; estructura de retención; capa impermeable; Puntos clave del control de la tarjeta
En los proyectos de Foundation Pit, la construcción correcta de impermeabilización es crucial para la estructura general, y también tendrá un gran impacto en la vida útil del edificio. Por lo tanto, los proyectos de impermeabilización ocupan una posición muy importante en el proceso de construcción de los pozos de base profundos. Este documento combina principalmente las características del proceso de construcción de Pit Foundation de Deep Foundation de los proyectos de construcción de Nanning Metro y Hangzhou South Station para estudiar y analizar la tecnología de impermeabilización de la Fundación Profunda, con la esperanza de proporcionar cierto valor de referencia para proyectos similares en el futuro.
1. Estructura de retención de impermeabilización
(I) Características de parto de agua de varias estructuras de retención
La estructura de retención vertical alrededor del pozo de base profundo generalmente se llama estructura de retención. La estructura de retención es un requisito previo para garantizar la excavación segura del pozo de base profundo. Hay muchas formas estructurales utilizadas en pozos de cimientos profundos, y sus métodos de construcción, procesos y maquinaria de construcción utilizada son diferentes. Los efectos de parpadeo de agua logrados por varios métodos de construcción no son los mismos, consulte la Tabla 1 para más detalles
(Ii) precauciones de impermeabilización para la construcción de paredes conectadas a tierra
La construcción de la fundación de la estación Nanhu de Nanning Metro adopta una estructura de pared conectada al suelo. La pared conectada al suelo tiene un buen efecto de impermeabilización. El proceso de construcción es similar al de las pilas aburridas. Se deben tener en cuenta los siguientes puntos
1. El punto clave del control de calidad de impermeabilización se encuentra en el tratamiento articular entre las dos paredes. Si se pueden comprender los puntos clave de la construcción del tratamiento articular, se logrará un buen efecto de impermeabilización.
2. Después de que se forma la ranura, las caras finales del concreto adyacente deben limpiarse y cepillarse hasta el fondo. El número de cepillados de pared no debe ser menos de 20 veces hasta que no haya barro en el cepillo de pared.
3. Antes de bajar la jaula de acero, se instala un pequeño conducto al final de la jaula de acero a lo largo de la dirección de la pared. Durante el proceso de instalación, la calidad de la junta se controla estrictamente para evitar que las fugas obstruyan el conducto. Durante la excavación del pozo de base, si se encuentra fugas de agua en la junta de la pared, la lechada se realiza desde el pequeño conducto.
(Iii) Enfoque de impermeabilización de la construcción de pilotes de fundición en el lugar
Algunas estructuras de retención de la estación Hangzhou South adoptan la forma de pila de fundición en el lugar aburrida + cortina de pila de chorro rotativo de alta presión. El control de la calidad de la construcción de la cortina de parada de agua de la pila de chorro rotativo de alta presión durante la construcción es el punto clave de impermeabilización. Durante la construcción de la cortina de parada de agua, el espacio de la pila, la calidad de la suspensión y la presión de inyección deben controlarse estrictamente para garantizar que se forme una correa impermeable cerrada alrededor de la pila de fundición en el lugar para lograr un buen efecto de impermeabilización.
2. Control de excavación de pozo de base
Durante el proceso de excavación de pozo de base, la estructura de retención puede filtrarse debido al tratamiento inadecuado de los nodos de la estructura de retención. Para evitar los accidentes causados por la fuga de agua de la estructura de retención, se deben observar los siguientes puntos durante el proceso de excavación de pozo de base:
1. Durante el proceso de excavación, la excavación ciega está estrictamente prohibida. Preste mucha atención a los cambios en el nivel del agua fuera del pozo de base y la filtración de la estructura de retención. Si se produce un brote de agua durante el proceso de excavación, la posición de brote debe rellenarse en el tiempo para evitar la expansión y la inestabilidad. La excavación solo se puede continuar después de adoptar el método correspondiente. 2. Se debe manejar el agua de filtración a pequeña escala en el tiempo. Limpie la superficie del concreto, use cemento de alta resistencia para sellar la pared y use un pequeño conducto para drenar para evitar que el área de fuga se expanda. Después de que el cemento de sellado alcanza la resistencia, use una máquina de lechada con presión de lechada para sellar el pequeño conducto.
3. Istustre de la estructura principal
La impermeabilización de la estructura principal es la parte más importante de Deep Foundation Pit Waterpusting. Al controlar los siguientes aspectos, la estructura principal puede lograr un buen efecto de impermeabilización.
(I) Control de calidad de concreto
La calidad del concreto es la premisa para garantizar la impermeabilización estructural. La selección de materias primas y el diseñador de la relación de mezcla aseguran las condiciones de soporte de la calidad del concreto.
El agregado que ingresa al sitio debe inspeccionarse y aceptarse de acuerdo con los "estándares para los métodos de calidad e inspección de arena y piedra para el concreto ordinario" para el contenido de lodo, el contenido de bloque de lodo, el contenido similar a la aguja, la clasificación de partículas, etc. Asegúrese de que el contenido de arena sea lo más bajo posible bajo la premisa de cumplir con la fuerza y la trabajadora laboral, para que haya suficiente grosor agregado en el concreto. La relación de mezcla de componentes de concreto debe cumplir con los requisitos de resistencia del diseño de la estructura de concreto, la durabilidad en varios entornos y hacer que la mezcla de concreto tenga propiedades de trabajo, como flujo de flujo que se adapta a las condiciones de construcción. La mezcla de concreto debe ser uniforme, fácil de compacta y anti-segregación, que es la premisa para mejorar la calidad del concreto. Por lo tanto, la trabajabilidad del concreto debe estar completamente garantizada.
(Ii) Control de construcción
1. Tratamiento de concreto. La junta de construcción se forma en la unión del concreto nuevo y viejo. El tratamiento en rugo aumenta efectivamente el área de unión del concreto nuevo y antiguo, lo que no solo mejora la continuidad del concreto, sino que también ayuda a la pared a resistir la flexión y el corte. Antes de verter concreto, la suspensión limpia se extiende y luego se recubre con material cristalino antie sepage a base de cemento. El material cristalino antie sepage a base de cemento puede unir bien los espacios entre el concreto y evitar que el agua externa se invade.
2. Instalación de Waterstop de placa de acero. La placa de acero de la mueca debe estar enterrada en el medio de la capa de estructura de concreto vertida, y las curvas en ambos extremos deben enfrentar la superficie orientada al agua. La placa de acero de la hendidera de la junta de construcción de la correa de la pared exterior posterior a la correa de clasificación debe colocarse en el medio de la pared exterior de concreto, y la configuración vertical y cada placa de acero horizontal de agua se deben soldar firmemente. Después de que se determina la elevación horizontal de la hiter Waterstop de la placa de acero horizontal, se debe dibujar una línea en el extremo superior de la hiterantía de la placa de acero de acuerdo con el punto de control de elevación del edificio para mantener su extremo superior recto.
Las placas de acero se fijan mediante soldadura de barras de acero, y las barras de acero oblicuas se soldan a la palanca de trabajo superior para fijar. Las barras de acero cortas están soldadas debajo de la hiterantía de la placa de acero para soportar la placa de acero. La longitud debe basarse en el grosor de la malla de acero de la pared de losa de concreto y no debe ser demasiado larga para evitar la formación de canales de filtración de agua a lo largo de las barras cortas de acero. Las barras de acero cortas generalmente están separadas no más de 200 mm de distancia, con un juego a la izquierda y a la derecha. Si el espacio es demasiado pequeño, el costo y el volumen de ingeniería aumentarán. Si el espaciado es demasiado grande, la hiterantía de la placa de acero es fácil de doblar y es fácil de deformarse debido a la vibración al verter concreto.
Las juntas de la placa de acero están soldadas y la longitud de la vuelta de las dos placas de acero no es inferior a 50 mm. Ambos extremos deben estar completamente soldados, y la altura de la soldadura no es menor que el grosor de la placa de acero. Antes de soldar, se debe realizar una soldadura de prueba para ajustar los parámetros actuales. Si la corriente es demasiado grande, es fácil quemar o incluso quemar a través de la placa de acero. Si la corriente es demasiado pequeña, es difícil iniciar el arco y la soldadura no es firme.
3. Instalación de tiras de agua que expanden el agua. Antes de colocar la franja de agua que sale de agua, barre la escoria, el polvo, los escombros, etc., y exponga la base dura. Después de la construcción, vierta las articulaciones de construcción de tierra y horizontal, expanda la tira de agua que sale de agua a lo largo de la dirección de extensión de la articulación de la construcción y usa su propia adhesividad para pegarla directamente en el medio de la junta de construcción. La superposición de la junta no debe ser inferior a 5 cm, y no se deben dejar puntos de interrupción; Para la junta de construcción vertical, se debe reservar primero una ranura de posicionamiento poco profundo, y la franja de hendedura debe integrarse en el surco reservado; Si no hay un surco reservado, las uñas de acero de alta resistencia también se pueden usar para fijar, y usar su autoadhesividad para pegarlo directamente en la interfaz de la junta de construcción, y compactarlo uniformemente cuando se encuentra con papel de aislamiento. Después de que se fija la tira de agua, arrances el papel de aislamiento y vierte el concreto.
4. Vibración de concreto. El tiempo y el método de vibración concreta deben ser correctos. Debe vibrar densamente pero no sobrevibrado o filtrado. Durante el proceso de vibración, la salpicadura del mortero debe minimizarse, y el mortero salpicado en la superficie interna del formulario debe limpiarse a tiempo. Los puntos de vibración de concreto se dividen desde el medio hasta el borde, y las varillas se colocan uniformemente, capa por capa, y cada parte del vertido del concreto debe vertirse continuamente. El tiempo de vibración de cada punto de vibración debe basarse en la superficie de concreto flotante, plano y no más burbujas que salen, generalmente 20-30s, para evitar la segregación causada por una vibración excesiva.
El vertido de concreto debe llevarse a cabo en capas y continuamente. El vibrador de inserción debe insertarse rápidamente y retirarse lentamente, y los puntos de inserción deben estar dispuestos y dispuestos en forma de floración de ciruela. El vibrador para vibrar la capa superior de concreto debe insertarse en la capa inferior de concreto en 5-10 cm para garantizar que las dos capas de concreto estén firmemente combinadas. La dirección de la secuencia de vibración debe ser lo más opuesta posible a la dirección del flujo de concreto, de modo que el concreto vibrado ya no ingrese al agua y burbujas libres. El vibrador no debe tocar las piezas y el trabajo de forma incrustada durante el proceso de vibración.
5. Mantenimiento. Después de verter el concreto, debe cubrirse y regarse en 12 horas para mantener el concreto húmedo. El período de mantenimiento generalmente no es inferior a 7 días. Para las piezas que no se pueden regar, se debe usar un agente de curado para el mantenimiento, o una película protectora debe rociarse directamente sobre la superficie del concreto después del desmoldeamiento, lo que no solo puede evitar el mantenimiento, sino también mejorar la durabilidad.
4. Tormado de capa impermeable
Aunque la impermeabilización del pozo de base profunda se basa principalmente en la resistencia a la auto-agua de concreto, la colocación de la capa impermeable también juega un papel vital en los proyectos de impermeabilización del pozo de base profunda. Controlando estrictamente la calidad de la construcción de la capa impermeable es el punto clave de la construcción impermeable.
(I) tratamiento de superficie base
Antes de colocar la capa impermeable, la superficie base debe tratarse de manera efectiva, principalmente para la planitud y el tratamiento de la filtración de agua. Si hay una filtración de agua en la superficie base, la fuga debe tratarse con enchufar. La superficie base tratada debe ser limpia, sin contaminación, sin gotas de agua y sin agua.
(Ii) Calidad de colocación de la capa impermeable
1. La membrana impermeable debe tener un certificado de fábrica, y solo se pueden usar productos calificados. La base de construcción impermeable debe ser plana, seca, limpia, sólida y no arenosa o pelada. 2. Antes de aplicar la capa impermeable, las esquinas de la base deben tratarse. Las esquinas deben convertirse en arcos. El diámetro de la esquina interna debe ser mayor de 50 mm, y el diámetro de la esquina exterior debe ser mayor de 100 mm. 3. La construcción de la capa impermeable debe llevarse a cabo de acuerdo con las especificaciones y los requisitos de diseño. 4. Procese la posición de la junta de construcción, determine la altura del vertido de concreto y realice un tratamiento de refuerzo impermeable en la posición de la junta de construcción. 5. Después de colocar la capa impermeable de la base, la capa protectora debe construirse a tiempo para evitar el hirviendo y perforar la capa impermeable durante la soldadura de la barra de acero y dañar la capa impermeable durante la vibración de concreto.
V. Conclusión
Los problemas comunes de penetración e impermeabilización de los proyectos subterráneos afectan seriamente la calidad general de la construcción de la estructura, pero no es inevitable. Principalmente aclaramos la idea de que "el diseño es la premisa, los materiales son la base, la construcción es la clave y la gerencia es la garantía". En la construcción de proyectos impermeables, el control estricto de la calidad de la construcción de cada proceso y tomar medidas preventivas y de control específicas seguramente alcanzará los objetivos esperados.
Tiempo de publicación: agosto-13-2024